Learning How Baseball Bats are Made at the Hoosier Bat Company
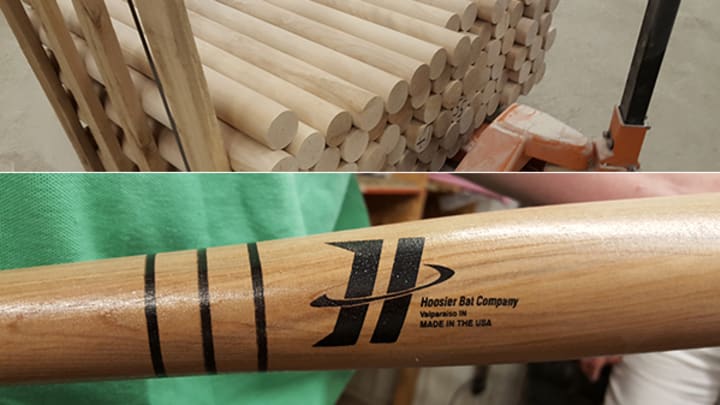
Baseball playoffs are right around the corner, and most fans are talking about pitching rotations, teams who may be in the hunt for the pennant race, and which teams will secure a wild-card position. Do you think anyone is paying attention to the bats the players are using? Probably not. As a matter of fact, I had never personally given it much thought until I visited the Hoosier Bat Company.
I recently sat down with Dave and Debbie Cook, co-owners of the Hoosier Bat Company, located in my hometown of Valparaiso, Indiana. I wanted to learn how wooden bats are made, and the differences between wooden and aluminum equipment.
Dave, who began his career as a scout with the New York Yankees, heard players tell him that they were having a tough time adjusting from aluminum to wooden bats. So in 1991, he started Hoosier Bat Company and invented a bat with three pieces of wood called the WoodForce 2000. Over the years, the company has made bats for major league players all the way down to T-ball players.
Debbie explained that there are several types of wood used in bats, including hickory, birch, maple, and ash. Ash peels and flakes quickly, while hickory is a heavier, dense wood. Most wooden bats are made of birch and have a two-inch sweet spot.
When I walked into the factory where the bats are made, I heard loud sanding and grinding noises, accompanied by the smell of wood. There was a cart full of cylinder-shaped wood waiting to be made into a bat. As I looked to the back of the room, I could see Dave wearing a protective breathing mask while sanding a bat on his sanding machine.
When a shipment of wood comes in, it is weighed and sorted. Someone pulls a pattern bat out of the selection hanging on the wall and uses it to cut the same pattern into the new bat with a machine called a lathe. There are two pieces of wood on both ends of the bat to keep the ends safe while in the lathe. (Those are eventually removed.)
The WoodForce 2000 bat goes through a special process. It is made of three different types of wood. The top is made of soft maple, the middle is made of hickory, and the handle is made of birch or ash. After the wood is cut, the glue wheel is used to saturate the ridges with glue, and then the three pieces are hand-fitted together. It takes about a day to let it dry. Then the bat heads over to the lathe, the sander, the dipping and the finishing rooms.
Next we traveled over to the sanding machine and watched as Dave sanded the bats. This process made them look much smoother, like a final product.
They don’t like to waste materials at Hoosier Bat. The sawdust created is used to line horse stalls, and the ends of the bats — the parts that are used to protect the bat during cutting — are sold to the public for use in crafts and for fireplaces.
My favorite stop on my tour was the dipping room. This is where the bats get their color. There are several containers of different colored paints. Each bat gets dipped in a color, ranging from a clear stain to black, red, and brown. With each dip, 0.2 of an ounce in weight is added to the bat, which some players say makes a difference in their performance. A player will send a bat back if it is not the perfect weight. After being dipped two or three times, the bats are hung to dry.
Our last stop was the stamping room, where they finish up the bat. They use a small machine to stamp the bat with their logo and the town where it is made: Valparaiso, Indiana.
The most difficult part of the process to me seemed to be when they hand drew the three lines in between the handle and the barrel of each bat. There are only two people who can accomplish this part of the process.
Debbie explained that “the batter should always hit with the label up. The label on a wooden bat is put on the center of the weak side of the bat. That gives a better visual.”
The biggest difference between aluminum and wooden bats is that the ball comes off much faster from an aluminum bat.
There are three Hoosier Bats in the Baseball Hall of Fame in Cooperstown, New York: Sammy Sosa’s, Lance Johnson’s, and Prince Fielder’s. In the past, MLB players who have used Hoosier Bats include Frank Thomas, Josh Hamilton, and Bryce Harper. Frank Thomas would have one bat for practice and one for games. Every player goes through a different number of bats during the season.
The process of how a wooden bat is made is fascinating. Each step is labor intensive, but the final result is well worth it to the batter who owns it. If you are ever in Indiana, stop by and take a swing at Hoosier Bat, where baseball rules.
Photos: Matt Collins
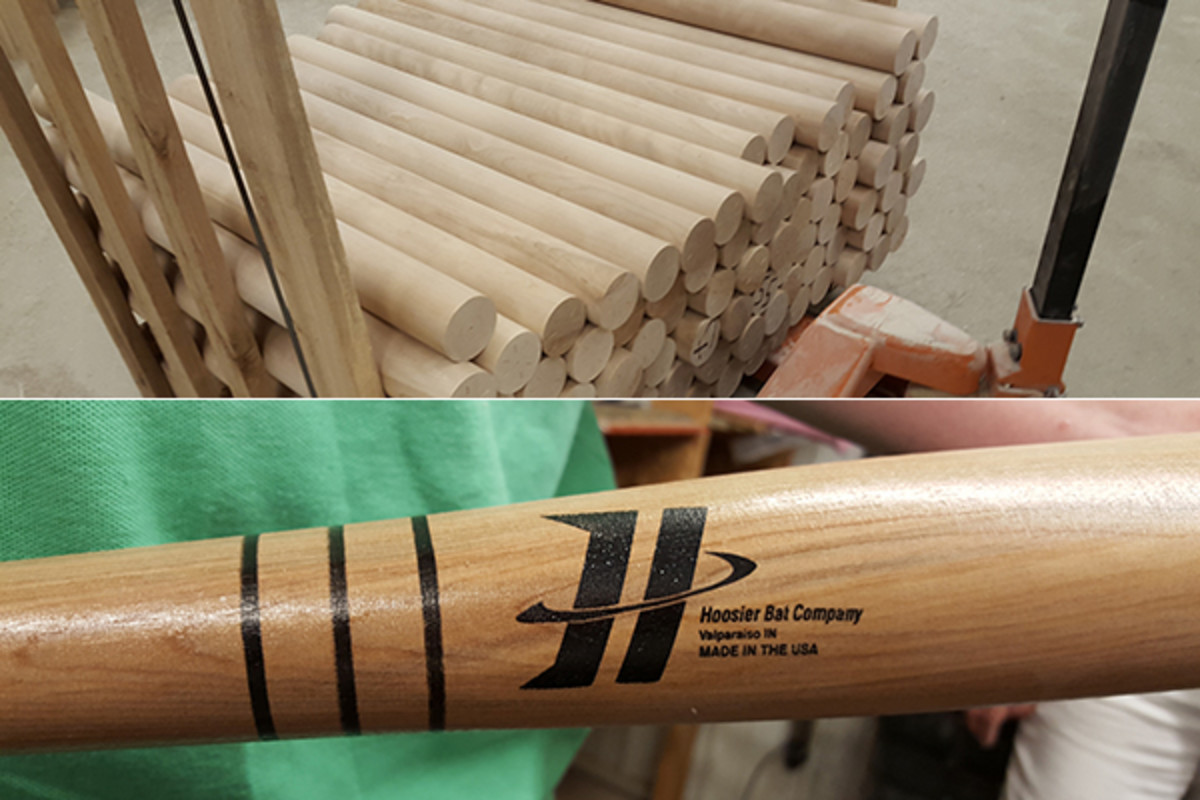
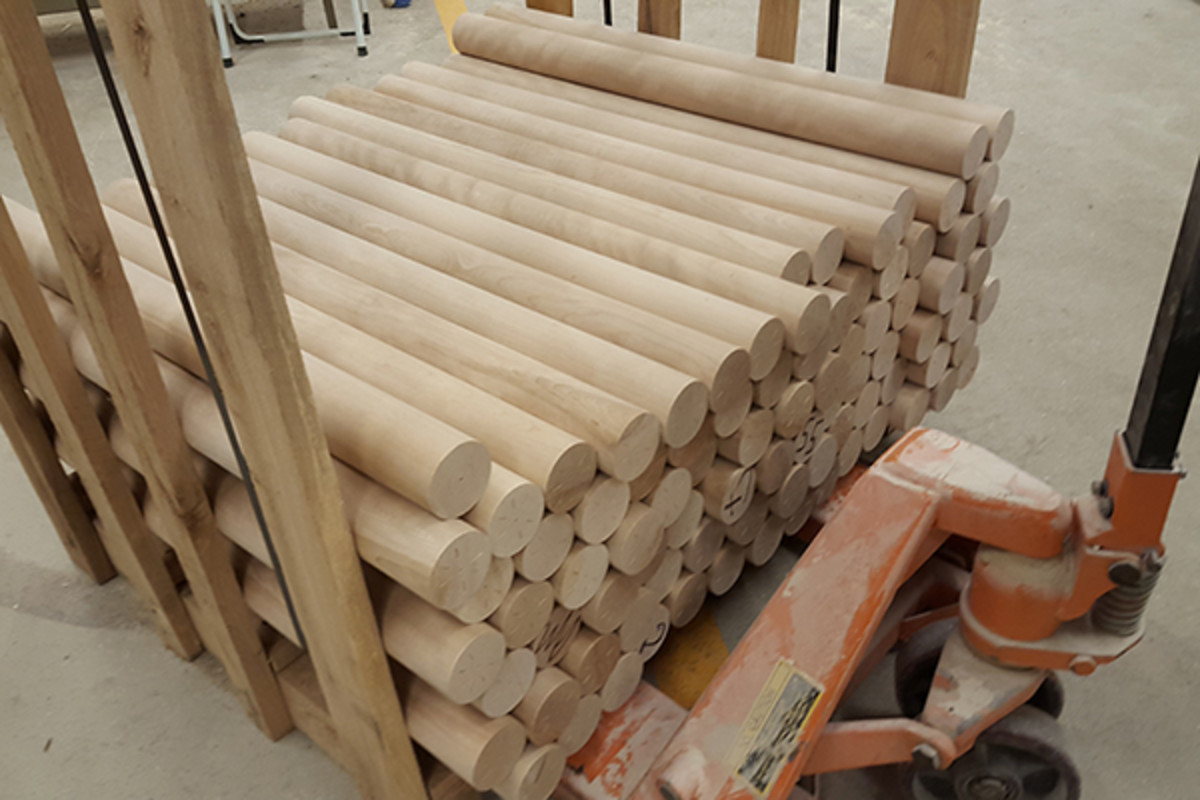
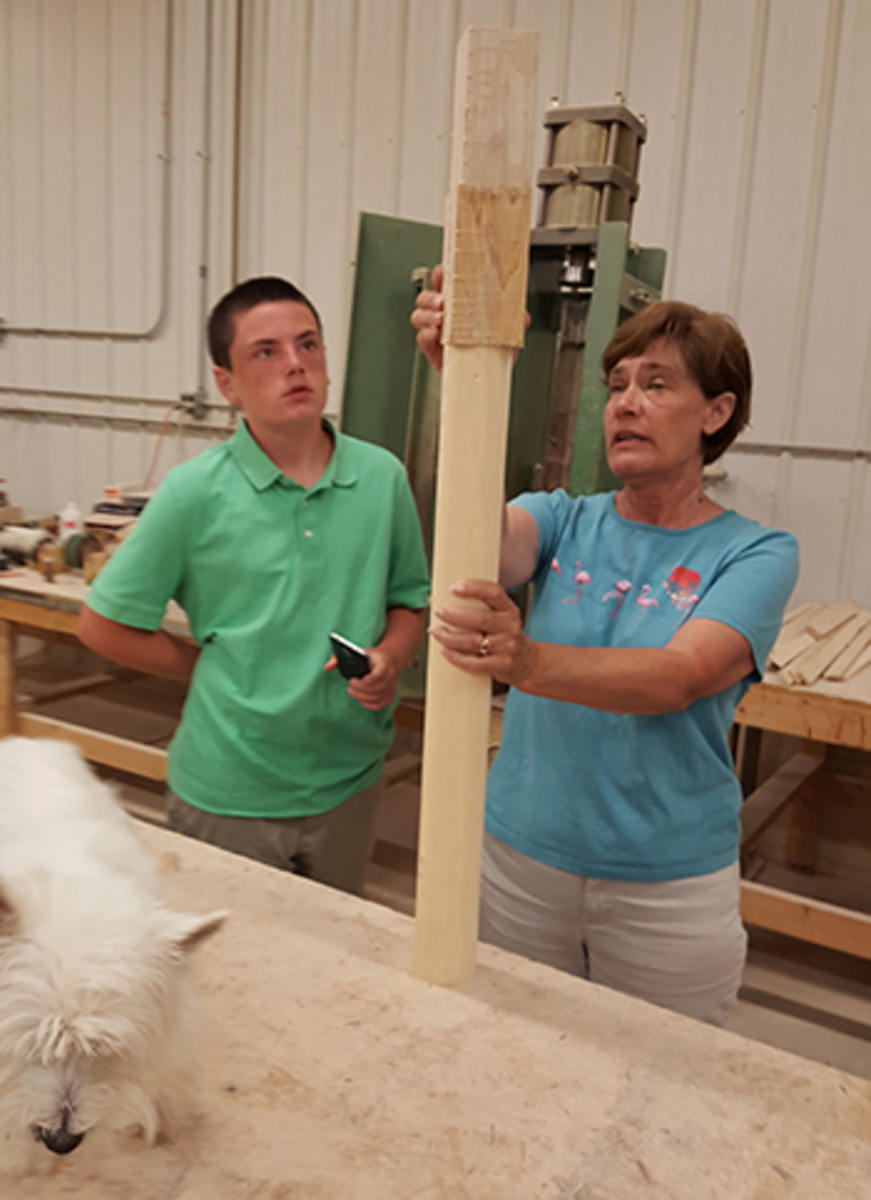
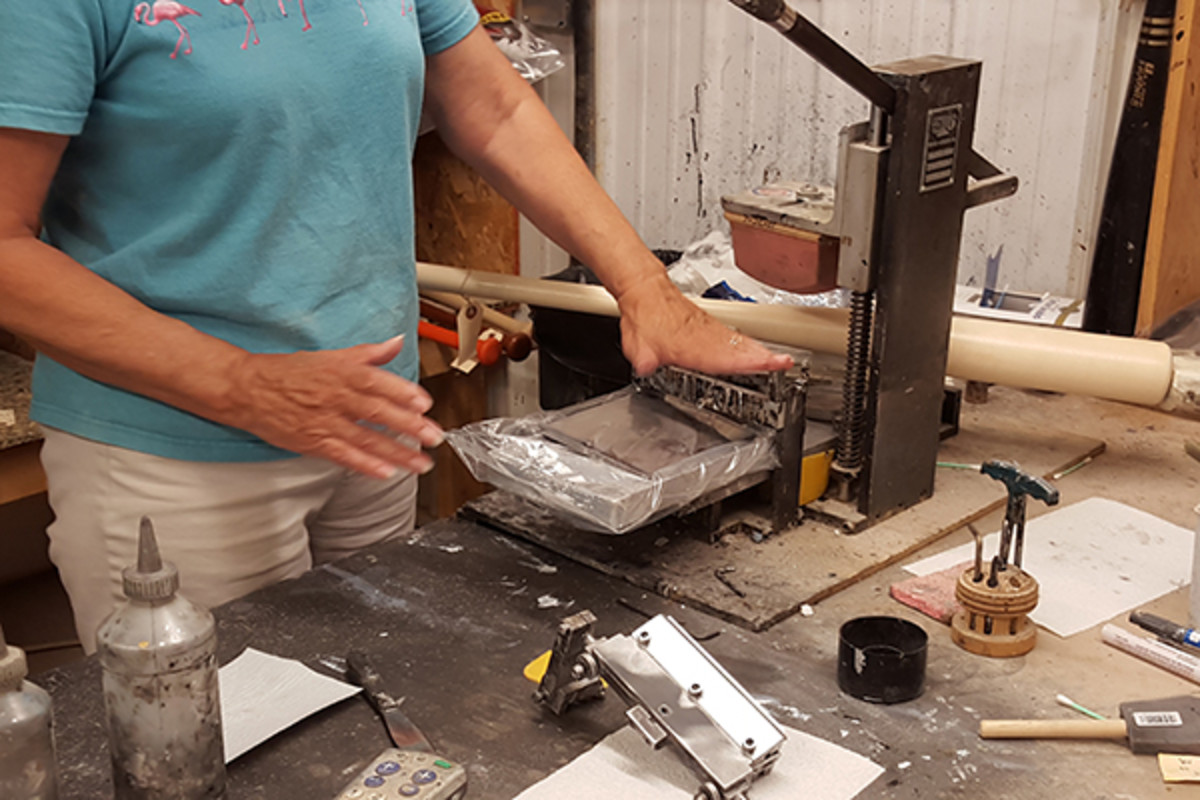